Apium P400:High Performance 3D Printing Solutions Customized for High Temperature PEEK
Integration of scientific research and production
3D printing with PEEK materials brings many technological advantages, opening up new possibilities and benefits in the fields of research and production:
1、excellent performance gains: PEEK materials for 3D printing applications can significantly enhance the performance of multiple advantages. These include superior corrosion resistance to withstand environmental erosion; reduced friction for lower energy loss; greater load bearing capacity for enhanced part durability; and strong resistance to oil, gas and chemicals. Notably, PEEK has a glass transition temperature (HDT) of 180°C at 0.45 MPa, making it stable in high-temperature environments.
2、More Flexibility in Design: 3D printing brings fewer constraints to the design of PEEK materials than traditional methods. Flexible processing makes it possible to print complex shapes, enabling engineers to improve system performance while reducing costs. This flexibility is difficult to achieve with traditional materials such as metals, for example to create curves or fluid patterns.
3、Significant weight reduction: The use of high-strength thermoplastics, such as PEEK, allows for significant weight reductions of up to 80% of the component using 3D printing or CNC machining. PEEK, for example, has a density of only 1.3 g/cm³, one-sixth that of steel and half that of aluminum. This lightweighting significantly reduces maintenance, logistics and installation costs, and thermoplastic parts can be up to one-sixth lighter than fast-molded metal parts.
4、Efficient utilization of material resources: 3D printing and CNC machining of thermoplastic materials such as PEEK are more energy-efficient in product development, effectively reducing waste. These materials can be melted, hardened, re-melted and re-hardened without generating waste, maximizing the use of resources.
As you can see, 3D printing PEEK material is not an easy task, it is a complex process that needs to follow strict parameters, and only well-designed, robust, durable, high-quality, professional 3D printers are up to the task. the Apium P400 3D printer is designed to cope with the printing requirements of these high-performance materials, which not only meets the complex printing parameters, but also ensures high-temperature environmental stability, providing strong support for 3D printing PEEK materials.
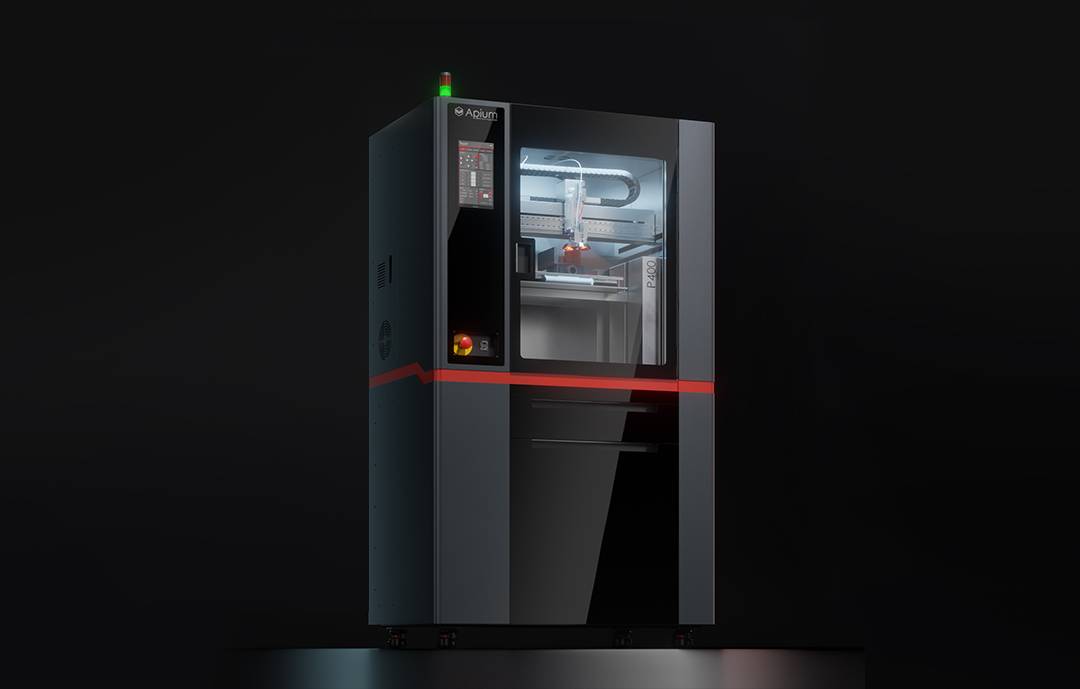
First, maintain a stable zone temperature. 3D printing of PEEK requires that the temperature be maintained within a tight range and not disturbed by outside temperature fluctuations.
Second, the use of a closed fabrication chamber is indispensable.3D printing of PEEK needs to be performed in a high-temperature environment, usually between 370° and 450° Celsius. At the same time, the temperature of the build plate should be kept above 120°. These stringent temperature requirements are not only for material suitability, but also to ensure print quality and part stability.
Even if the 3D printer is specifically designed to withstand the high temperatures of PEEK, it is important to ensure that it is installed in an environment that is not affected by sudden temperature changes. A stable environment will help you fully utilize the printer's performance and avoid unexpected problems caused by heating, cooling, and other factors.
These key data and practical experience are essential to successfully meeting the challenges of 3D printing on PEEK, and the Apium P400, a 3D printer designed for high-temperature 3D printing on PEEK, is carefully built with these requirements in mind to ensure good results in the application of high-performance materials.
1、New Generation Heating System: The strength of 3D printed polymers has always been a technical difficulty and bottleneck towards application scenarios. However, the Apium P400 introduces a new generation of Zone Conformal Heating System that skillfully solves this problem. With a maximum heating temperature of 540°C, this system heats the printed layers by following the shape of the radiation, realizing the formation of molecular entanglement between layers of polymer materials such as PEEK during the cooling process of the print and having the same structural and mechanical strength as the profile after crystallization.
2、Precise environmental control: While enabling the integration of research and production, the Apium P400 provides a stable temperature environment for the printing process through the design of the stabilized heating zones and the closed manufacturing chamber. This environmental control not only ensures the print quality of high temperature materials, but also enables the user to achieve consistently excellent results for different needs.
3、High Precision Printing Technology: The technical excellence of the Apium P400 is also reflected in its precision printing technology. From extrusion to layer thickness control, every step of the process is carefully engineered to ensure the high quality and precision of the printed part. This not only meets the precise requirements of scientific research, but also adapts to product-level manufacturing standards.
4、Research and production in one: The Apium P400 has been designed to emphasize the close integration of research and production. It not only meets the needs of researchers for high-temperature PEEK and other materials, but also demonstrates its excellent stability and efficiency in the production environment. This makes the transition from scientific research to practical application much smoother, providing users with a one-stop solution.
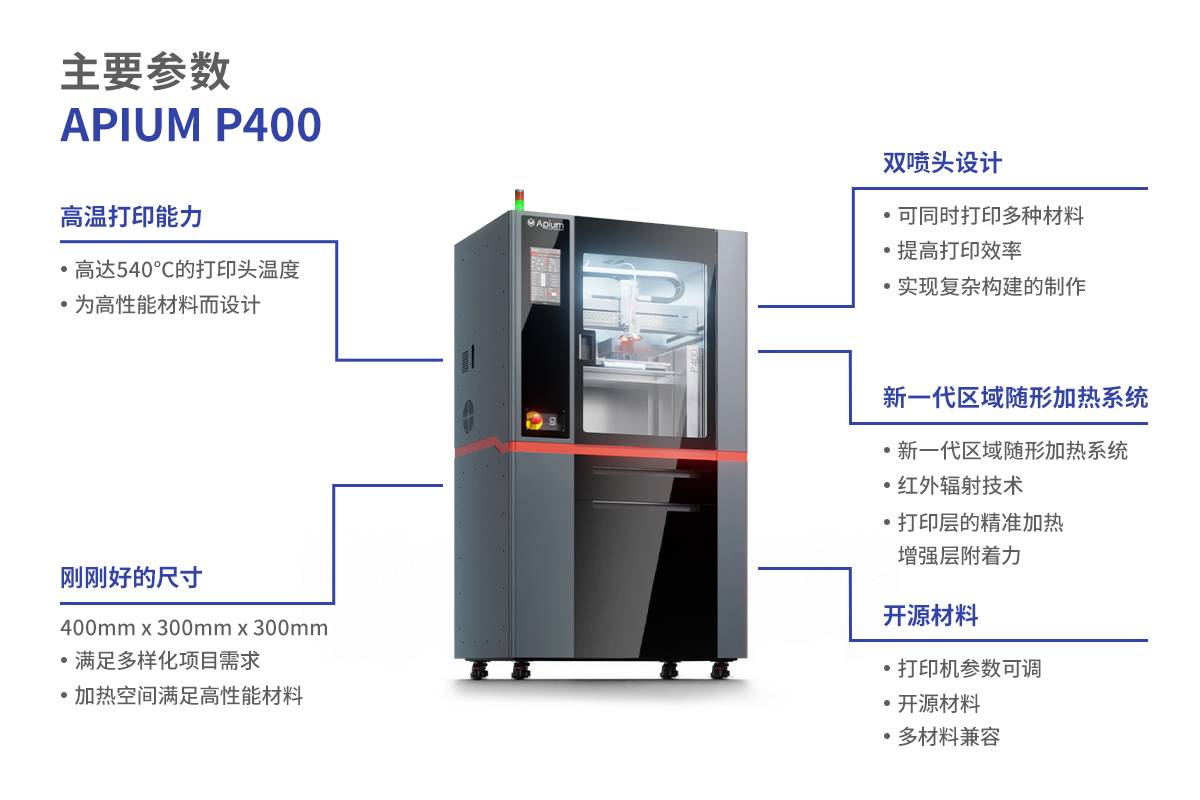
1、Automotive: The high heat and wear resistance of PEEK materials provides superior performance in the manufacture of engine components, friction brake linings and driveline parts. Its heat deflection temperature and coefficient of friction benefits allow it to withstand high engine temperatures while reducing energy loss and heat buildup in braking and driveline systems. In addition, PEEK's chemical stability makes it suitable for use in the manufacture of cooling system components and fluid storage containers, helping to maintain system reliability and longevity.
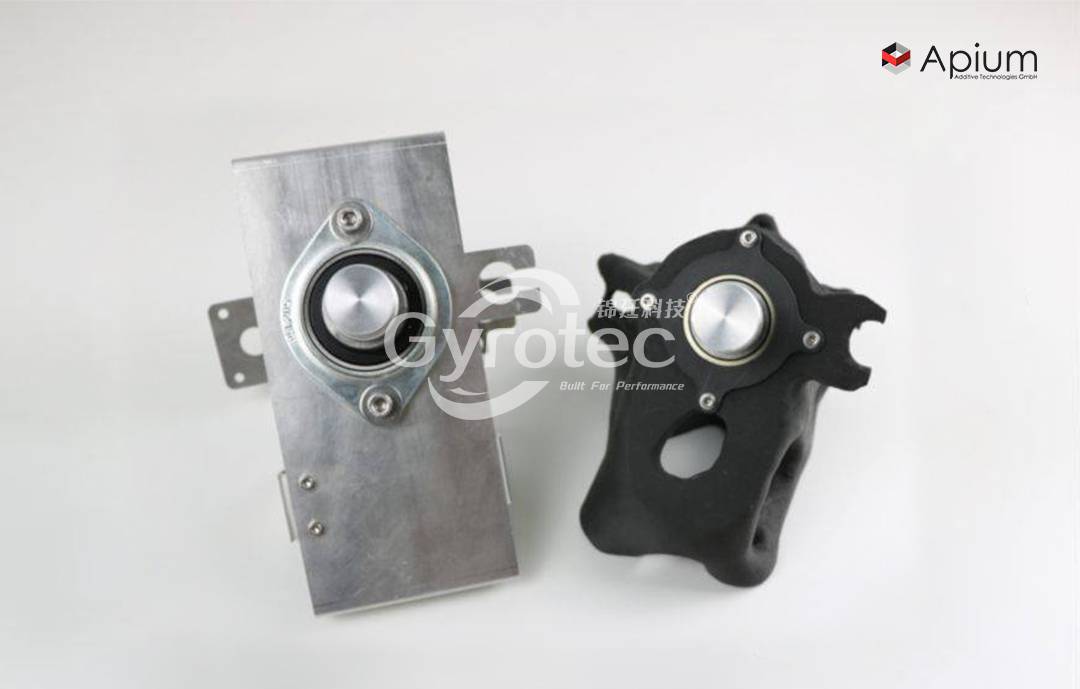
Automotive Research Case Diagram
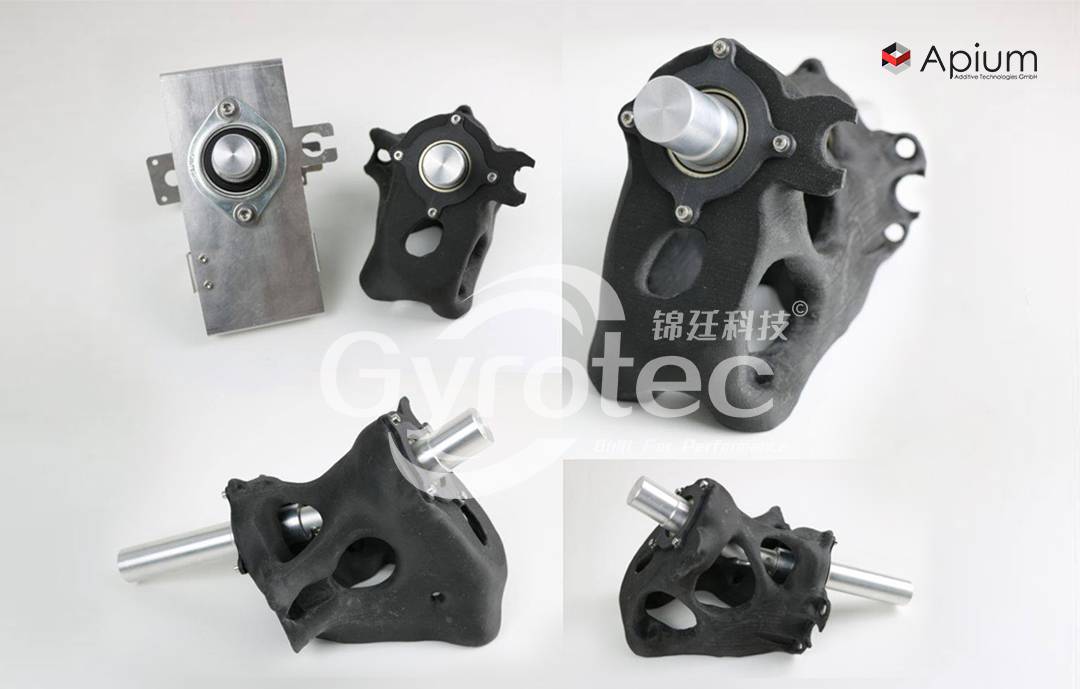
Automotive Production Case Diagram
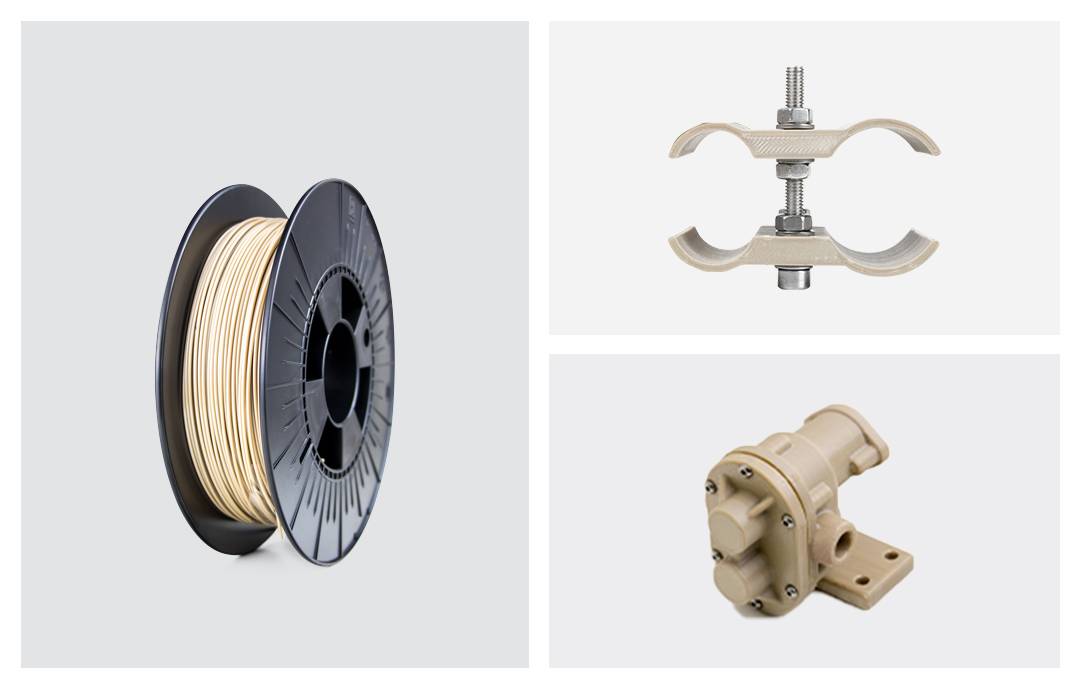
Automotive Production Case Diagram
2、Aerospace: PEEK's molecular structure allows it to maintain excellent performance at high temperatures and in extreme environments. Its heat deflection temperature (HDT) of up to 180°C (at 0.45 MPa) makes it suitable for the manufacture of complex guidance systems and engine components, ensuring the stable operation of aircraft under extreme conditions. In addition, PEEK's low coefficient of thermal expansion and excellent mechanical properties make it ideal for manufacturing lightweight aerostructural components, contributing to improved fuel efficiency and performance of aircraft.
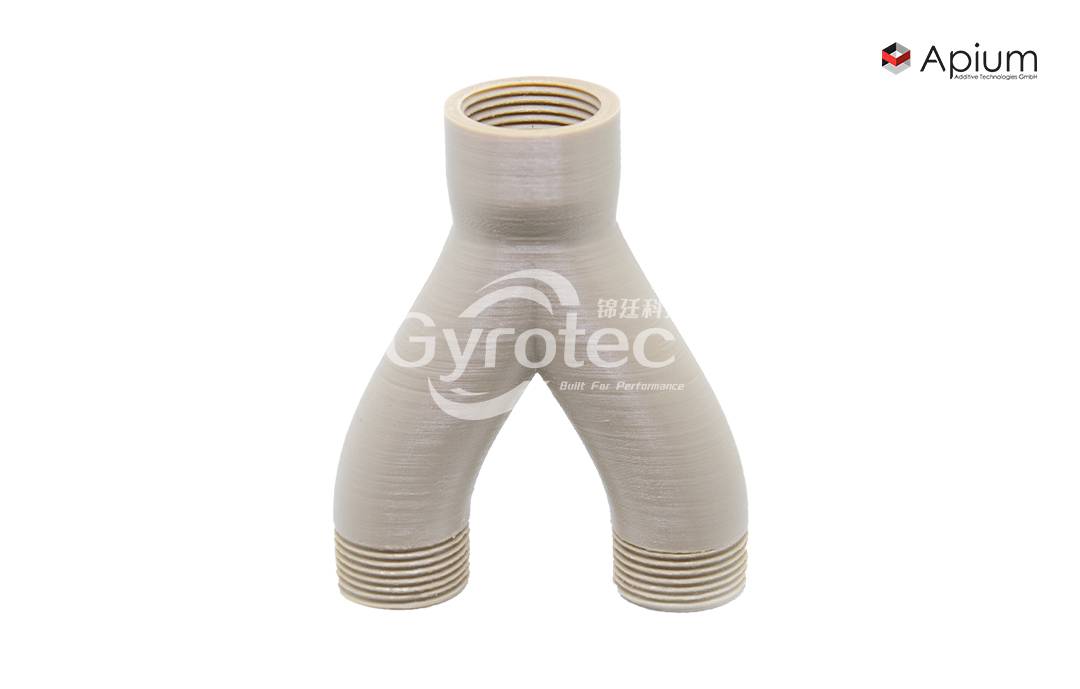
Aerospace research case map
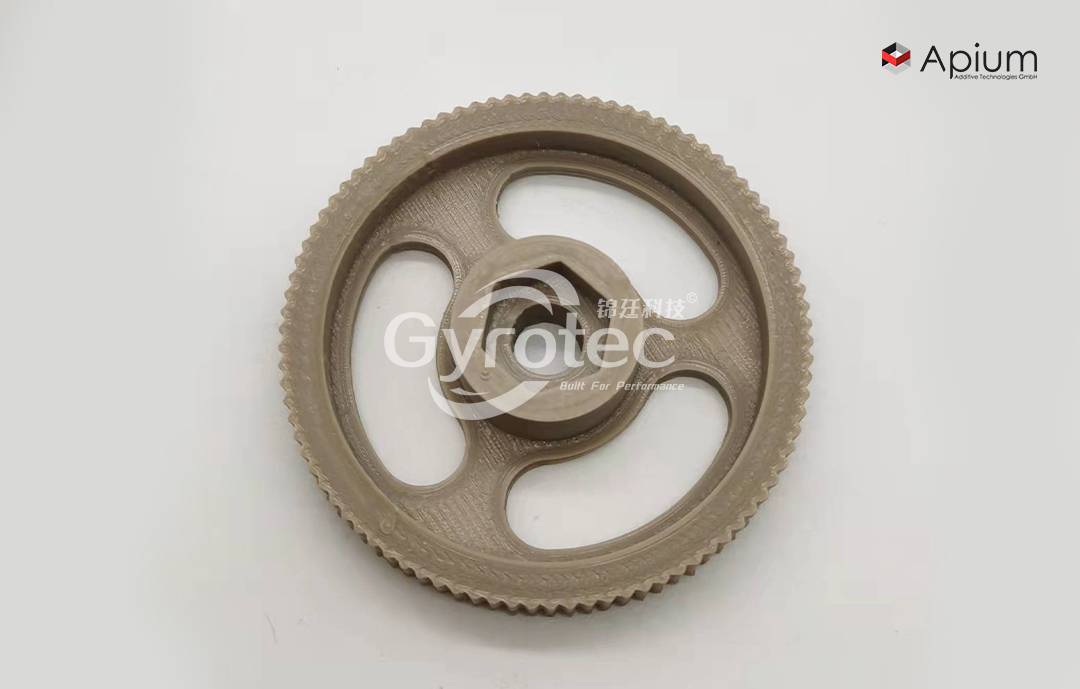
Aerospace production case map
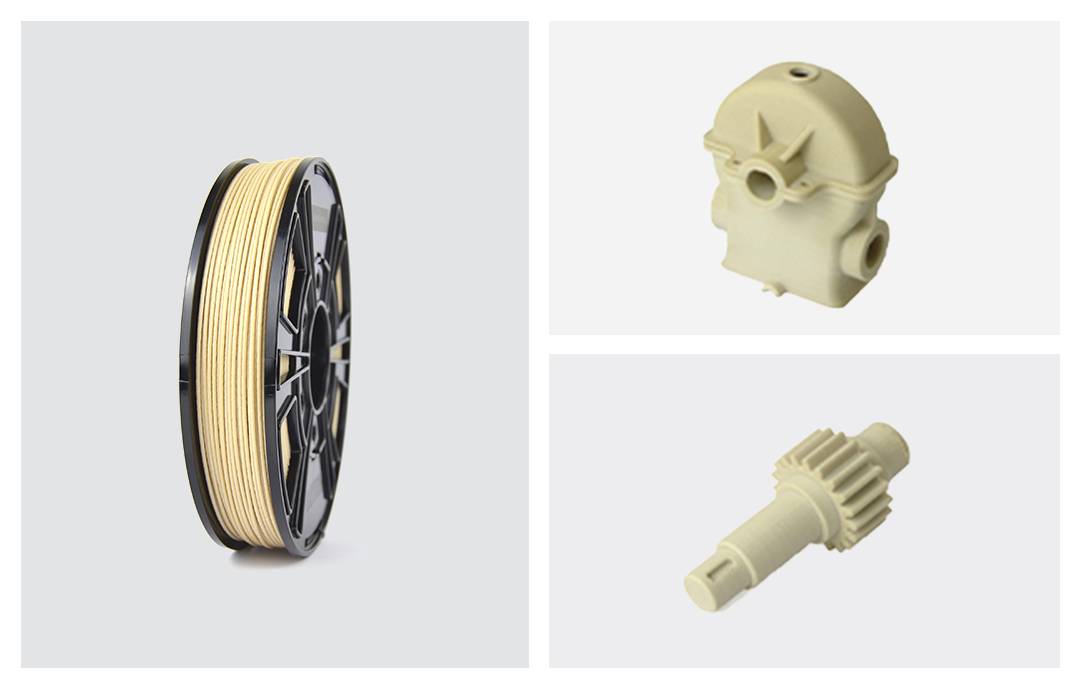
Aerospace production case map
3、Medical Industry: The biocompatibility and high strength properties of PEEK materials make them ideal for medical implants. Their stable molecular structure enables them to move catheters within the body while having a low coefficient of friction, which helps reduce tissue irritation. In addition, the chemical stability and corrosion resistance of PEEK materials make them suitable for use in the manufacture of medical device components and housings, ensuring the stability and reliability of the devices in the rigors of the medical environment.
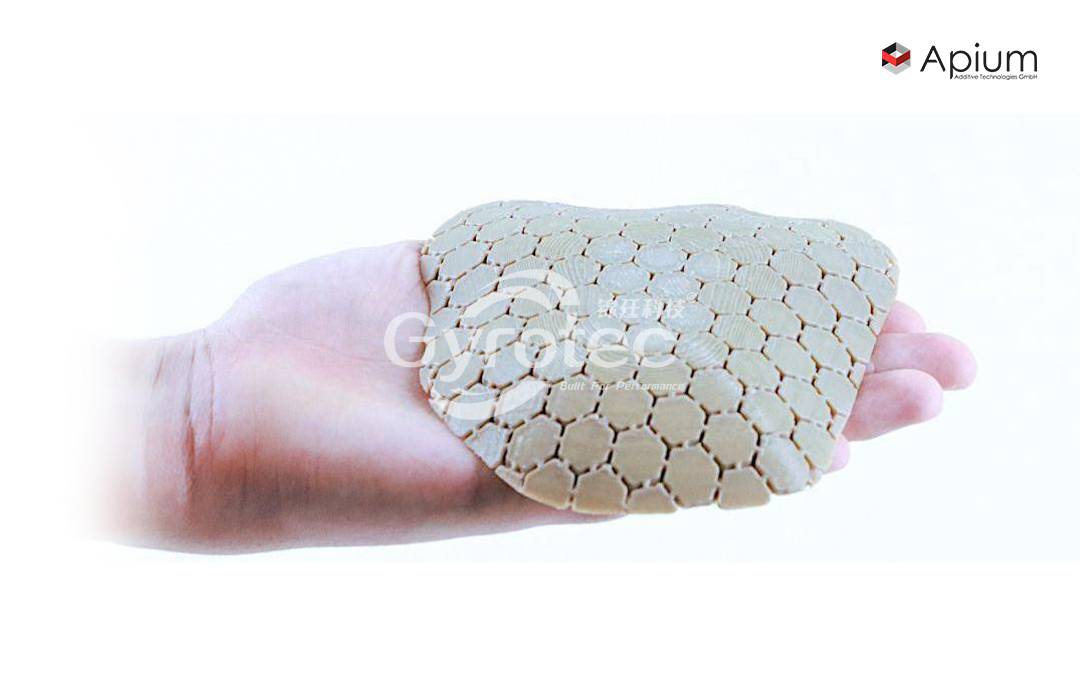
Medical Research Case Map

Medical production case map
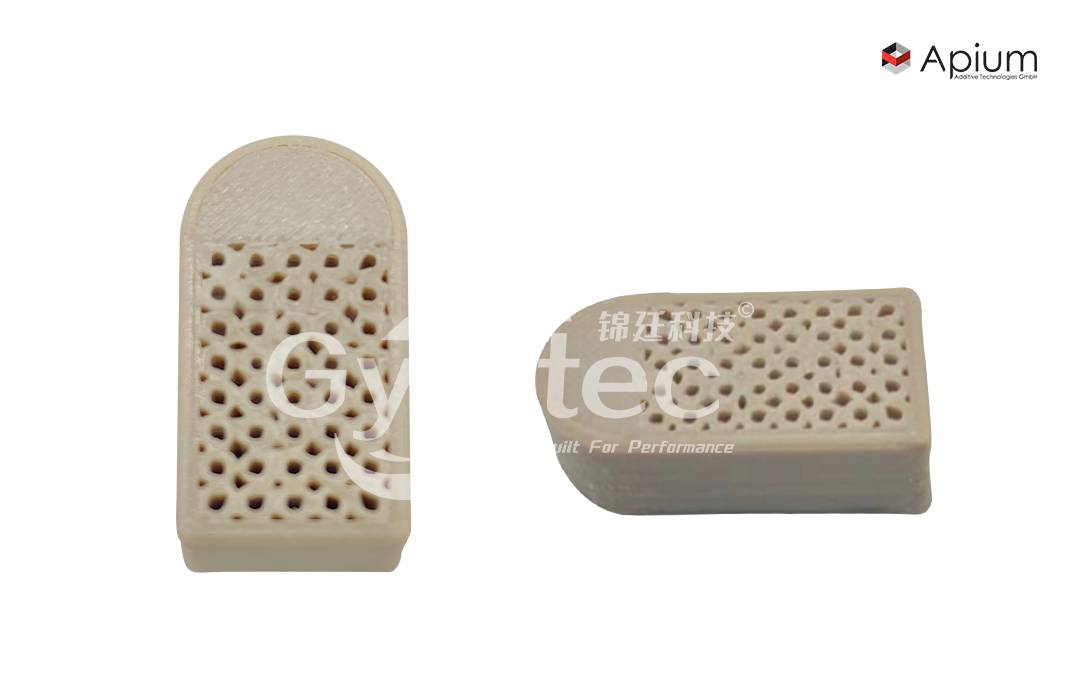
Medical production case map