革新航空引擎
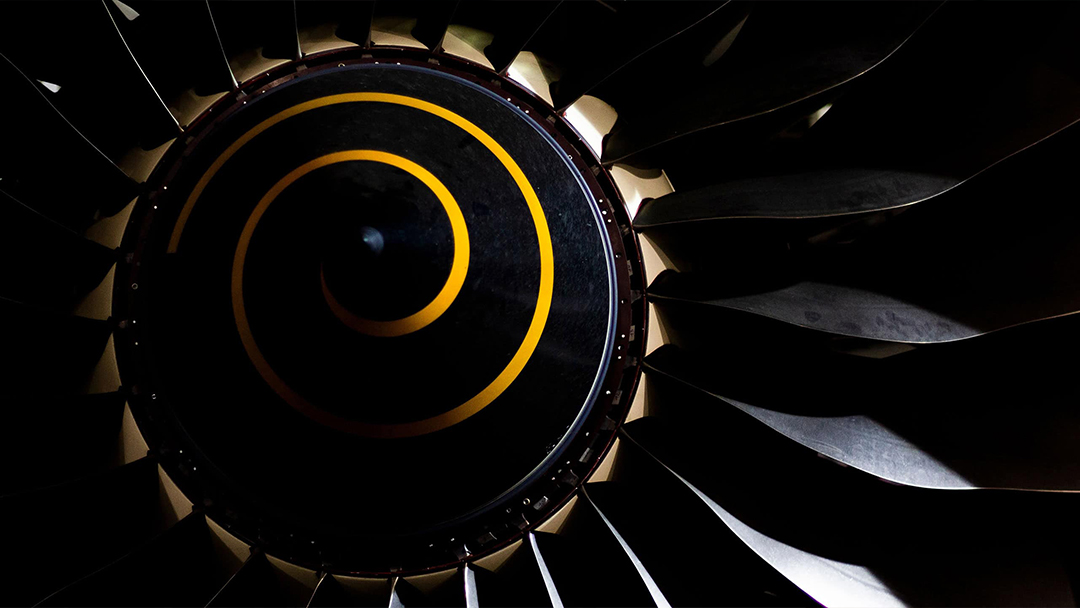
Science & Technology
快速成型技术正助力我们大幅缩短下一代涡扇发动机系列的研发周期,这一变革预示着飞行领域的未来将被重新定义。我们自豪地成为首批利用陶瓷3D打印技术制造涡轮叶片的喷气发动机制造商之一。
Honeywell的首席制造工程师Brian Baughman指出:“传统上,涡轮叶片依赖于精密的熔模铸造工艺,全球仅有少数铸造厂能够驾驭这种复杂技术。该工艺涉及制作高度复杂的金属模具及工具,用来塑造陶瓷模具,进而通过熔融超合金浇铸成形叶片。”
如今,我们采用了基于大容量容器的高精度3D打印技术,直接处理陶瓷浆料并打印模具。通过与3D打印领域先锋Prodways集团合作,运用其先进的3D打印机,我们显著减少了制造一级高压涡轮叶片所需的时间与成本。
首席研发科学家Mike Baldwin强调:“传统熔模铸造工艺下,仅为了研发需求制造涡轮叶片就可能耗时一至两年。而快速成型技术让我们能在短短七到八周内完成设计、模具打印、铸造、测试,并取得实测数据验证模型。设计上的任何调整均可通过电子方式迅速完成,新叶片六周左右即可问世。”
Baldwin补充道,以往即便对叶片设计进行细微调整,成本也非常高昂。“增材制造技术带来了快速原型制作的能力,大大增强了我们加速研发进程、控制成本并为客户提供优质产品的灵活性。缩短开发周期是我们的主要目标,同时,与传统叶片铸造相比,我们预期还能节约数百万美元的开发费用。”

加速未来飞行
Science & Technology
2023年,我们在Phoenix的增材制造中心安装了Prodways新一代DLP 3D打印机ProMaker Ceram Pro 365,这是自2016年开始的技术深度合作的新成果,进一步壮大了我们现有的Prodways L5000打印机阵容。
Prodways集团CEO Michaël Ohana表示:“我们的3D打印机与这类应用完好契合,能够在一天内处理陶瓷浆料,高效产出大量零件,并确保每次打印的一致性。”
Baughman认为,快速成型技术对于生产小批量的高精密部件尤为适宜。“涡轮叶片的传统模具成本高昂且制作周期长,使得小批量生产面临重重困难。在此背景下,快速成型制造展现出了巨大价值。”
Honeywell自2007年在Phoenix实验室首次涉足增材制造以来,已利用3D打印技术生产了数百种飞机部件,并将此行业领先的实践拓展至中国、欧洲、印度以及美国各地的业务中。
作为公务机、军用教练机和直升机涡轮发动机的领航供应商,我们正积极研发新一代涡轮风扇发动机,这些引擎将更加轻便、安静、动力强劲,并且能够使用100%可持续航空燃料。

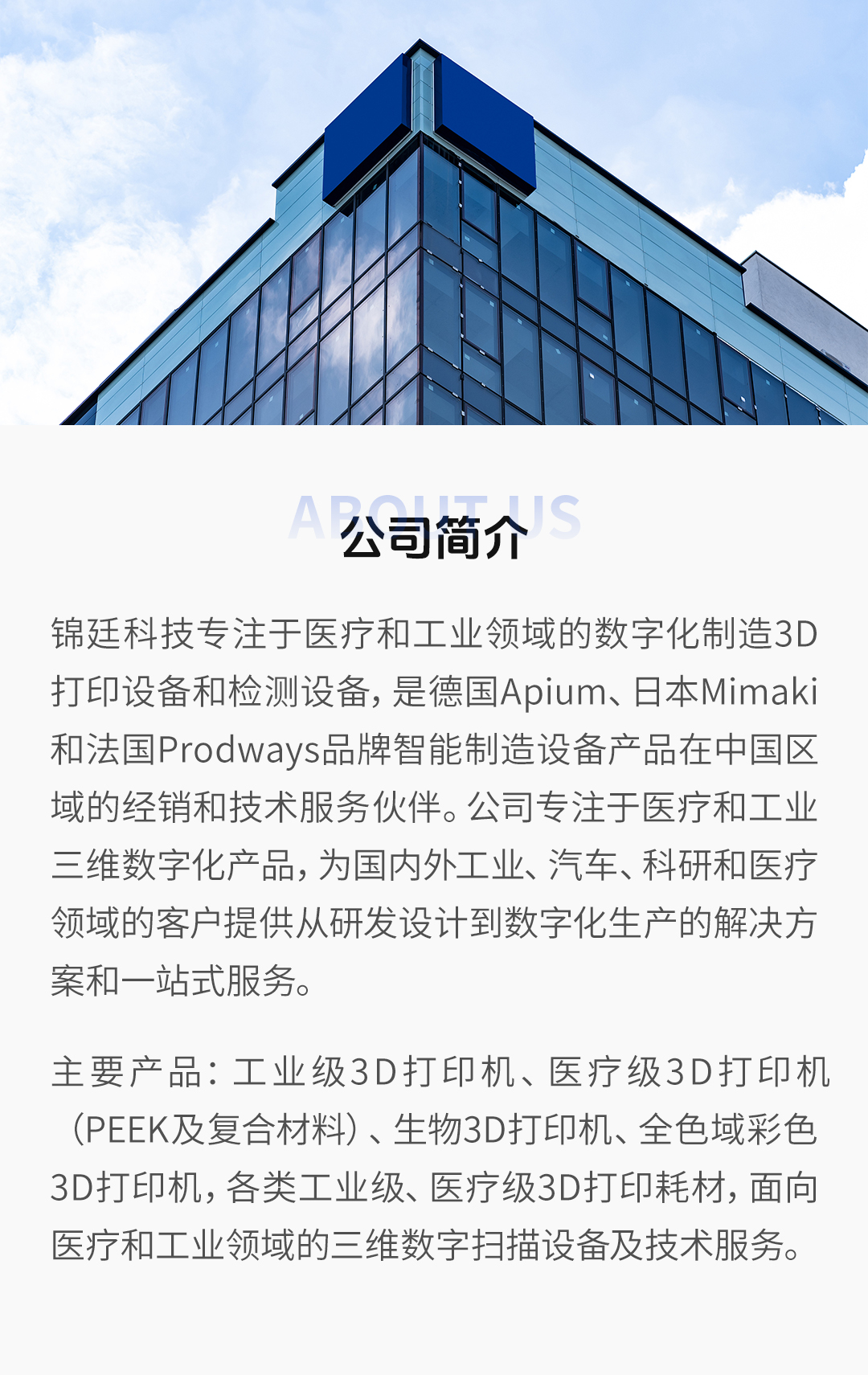
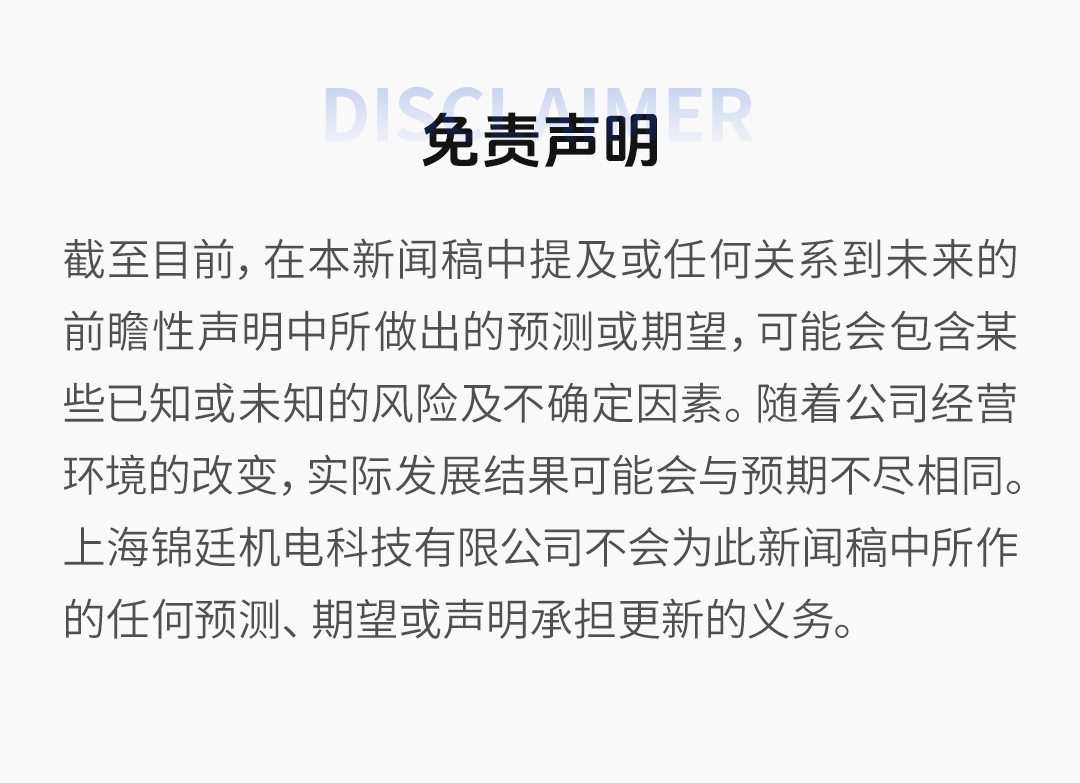